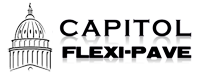
Specifications
SECTION 32 12 43 – FLEXIBLE POROUS PAVING
(Formerly Section 02795 Porous Pavement)
Download Here:
32 12 43 – Flexi-Pave, Porous Flexible Paving Spec v6.29 PDF Version
32 12 43 – Flexi-Pave, Porous Flexible Paving Spec v6.29 WORD Version